Sign in to follow this
Followers
0
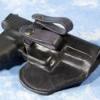
My First Avenger Holster
By
mlapaglia, in Gun Holsters, Rifle Slings and Knife Sheathes
By
mlapaglia, in Gun Holsters, Rifle Slings and Knife Sheathes