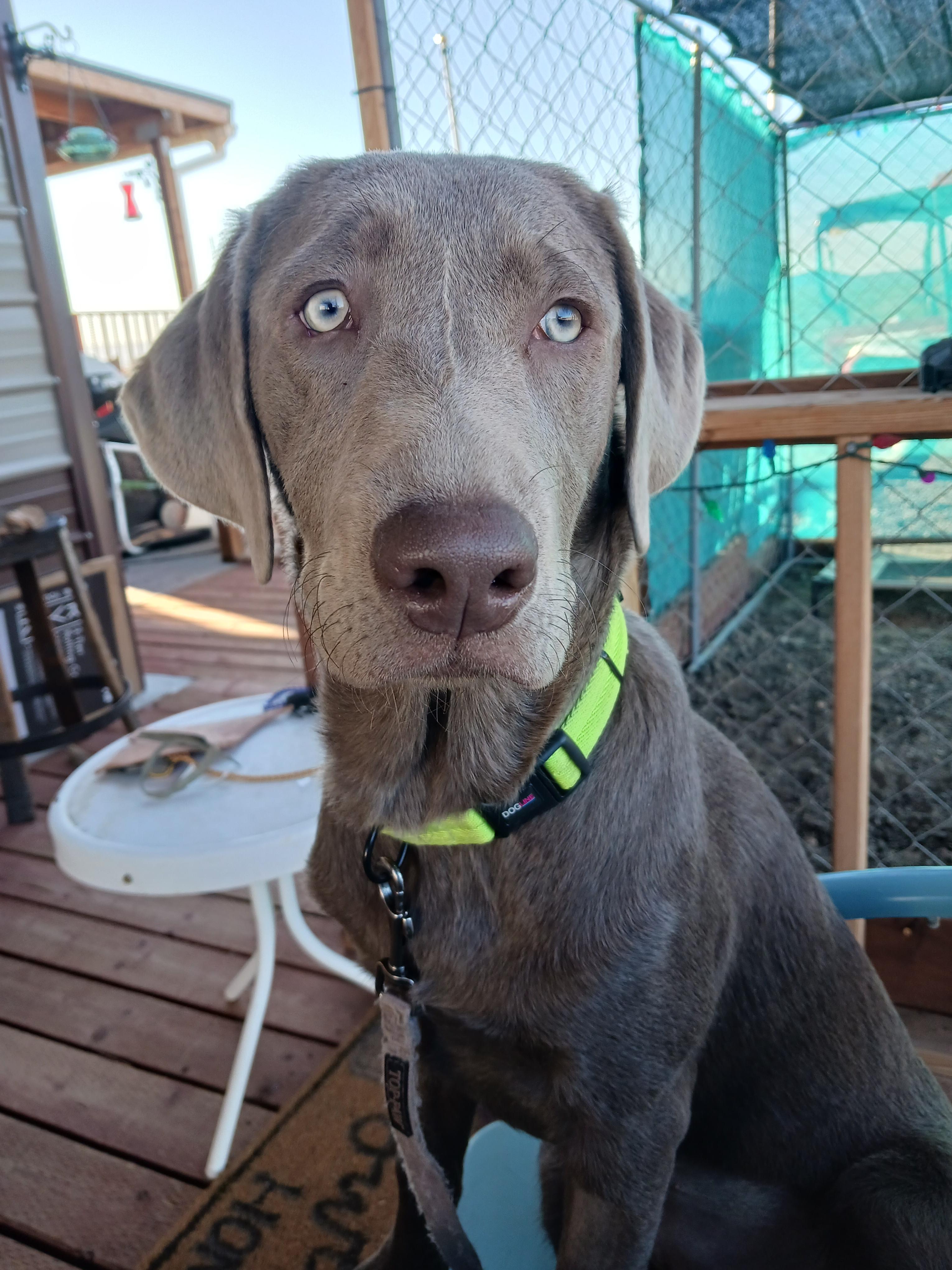
Southerngunner
Members-
Content Count
99 -
Joined
-
Last visited
About Southerngunner
-
Rank
Member
- Birthday 05/22/1953
Profile Information
-
Gender
Male
-
Location
Yucca Arizona
-
Interests
Family, Silver Labrador's,guns
LW Info
-
Leatherwork Specialty
Still trying to figure that one out.
-
Interested in learning about
The proper way to use sewing machines and work leather
-
How did you find leatherworker.net?
On google Researching old Singer 168w101 machine
Recent Profile Visitors
The recent visitors block is disabled and is not being shown to other users.
-
Anybody Ever Dealed With Levy Atlas Company?
Southerngunner replied to Jimbob's topic in Leather Sewing Machines
I would not hesitate to buy from him again everything about the purchase was amazing . He did what he said he would do and was professional and courteous through the whole deal. I would highly recommend if you are in the market for a machine that you give him a call -
Anybody Ever Dealed With Levy Atlas Company?
Southerngunner replied to Jimbob's topic in Leather Sewing Machines
Fast forward to 2024. This is an old thread but I think this is where my response belongs. I ordered an AT441 from Mr. Levy after talking to him on 2 or 3 occasions, he gave me a fantastic price and set the machine up the way that I wanted it. He changed the drive pulley on the servo to a 2" and included a bunch of needles, oil, and a giant spool of 210 thread. He said that he packed it up for shipping himself so it would get to my place without damage. It showed up fine yesterday and all that I had to do was get that big heavy rascal on the table and thread it. I was very pleased when it sewed good from the start. I need to figure out what I'm going to make on it now -
Does anyone have a cowboy cb 243
Southerngunner replied to Southerngunner's topic in Leather Sewing Machines
It has been picked up by the shipping company if they don't destroy it during transit I should see it in 5 to 7 days , my fingers are crossed . -
Does anyone have a cowboy cb 243
Southerngunner replied to Southerngunner's topic in Leather Sewing Machines
Well I guess it doesn't matter much anymore since I just bought a new 441 clone for a good price, waiting on delivery. -
I accidently ran across this machine while searching for a heavy sewing machine. I understand it is basicaly a 441 flatbed. I know that I can turn a 441 into a flatbed, I'm just more comfortable on my consew 206 than the cobra 26. In all fairness I haven't done a lot of sewing yet on my cylinder machine . Any input would be appreciated since the cost of either machine is similar.
-
I don't think that I can pass this deal up.
Southerngunner replied to Southerngunner's topic in Leather Sewing Machines
-
I don't think that I can pass this deal up.
Southerngunner replied to Southerngunner's topic in Leather Sewing Machines
Usually I'm a glutton for punishment as well but instead of hearing "I told you so" from the little lady for buying someone else's problem I passed on the 168W-101. I think that my next machine will be a new 441 style, if I'm going to get in trouble it's either going to be go big or stay on the porch. -
I don't think that I can pass this deal up.
Southerngunner replied to Southerngunner's topic in Leather Sewing Machines
Well I went to the shop today and took a closer look at the 168W-101. It did not have any knee or foot pedal presser lift option besides the one behind the needle bar. The front cover was missing and there was a broken off screw that would hold the plate. I had to screw around for almost an hour to get it to pick up the bobbin thread, the walking foot appeared to work properly as I got it to stitch eventually by turning the hand wheel. The drive belt didn't look like it was been replaced for several years as the edges showed some slight fraying. The owner of the shop hasn't touched it since it got there on consignment over 2 years ago and wanted to sell it as is. He did not have a belt for me to try it plugged in. There was enough little alarms going off in my head that I wasn't willing to take a chance with it ( I dont need another project that I propbably can't get parts for). It was a cool machine nonetheless and eventually I may end up with post machine just not today. It was probably worth the $250. But I did end up passing on it -
I don't think that I can pass this deal up.
Southerngunner replied to Southerngunner's topic in Leather Sewing Machines
Thanks for the explanation. -
I don't think that I can pass this deal up.
Southerngunner replied to Southerngunner's topic in Leather Sewing Machines
What is the difference between the g and the w models ? -
I don't think that I can pass this deal up.
Southerngunner replied to Southerngunner's topic in Leather Sewing Machines
After a year and a half of using my other machines I am comfortable enough to find my way around my first post machine. I still have a lot to learn but I'm not afraid to tear into one now and troubleshoot it. Thanks to the very knowledgeable and helpful folks on the forum, I'm sure that I will have some dumb questions before it's all said and done -
I don't think that I can pass this deal up.
Southerngunner replied to Southerngunner's topic in Leather Sewing Machines
As soon as I get it here and cleaned up the servo will be on the way if it doesn't need and other serious repairs -
I don't think that I can pass this deal up.
Southerngunner posted a topic in Leather Sewing Machines
My dealer still has this old Singer 168W-101 that I almost bought 1-1/2 years ago. I'm pretty sure that I don't need it since I already have ,a cobra 26, consew 206 rb -2, and a econosew 18"arm 29 k copy. I gave him a call today and he said that I could have it for $250.00 with the table clutch motor and light and bobbin winder. I'm supposed to go get it next week, he said he is tired of looking at it. I hope I'm not making a mistake. -
Cobra Class 26 Oil Resorvoir Pan
Southerngunner replied to rodneyv's topic in Leather Sewing Machines
My class 26 has the pan also, I believe it is a catch pan to keep excess oil from your table -
Thanks for your reply, I passed on that machine but it is still at the shop 1 1/2 years later. Every time that I stop in I'm tempted to ask about it just because it a cool vintage machine. But I am actually thinking of a cowboy 4500 or cobra class 4 to do more than my class 26 cobra can do, I also picked up an enconosew 18 inch arm shoe patcher copy of the singer 29 series..