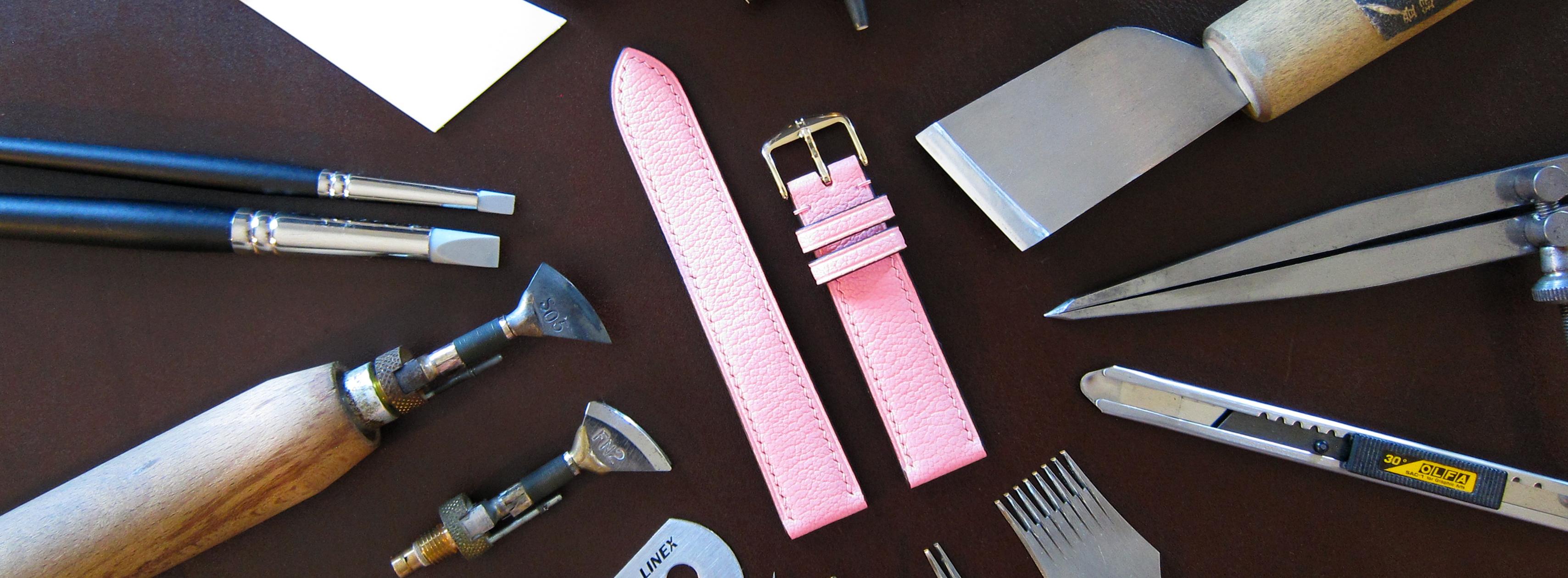
Danne
Members-
Content Count
772 -
Joined
-
Last visited
-
It have been slow with crafting lately, still haven't bought a skiving machine, looking at different alternatives when it comes to motors, I only need to buy a head, because I will mount it to my desk (you have maybe seen the pictures of my crafting area) I guess it will either be a Sieck (Chinese clone) and if needed replace feed wheel and bell knife, or a Fortuna SM-50 head.
-
Thank you, it's Tärnsjö 9368 https://tarnsjogarveri.com/leather/our-selection-of-leather/#tooling-sides
-
No, the color name is oranger if I remember correctly. Another leather that could be a good choice as strap lining is "swift calf" Not possible to order from the tannery (RMG Pomari) in low quantity, but when making straps at least I don't see any problems with spending a little bit more/sq.ft and buy from a reseller, because of the small amount needed.
-
Thank you. It's goat leather, Alran sully.
-
CalgaryJim started following Danne
-
Danne started following Why Ritza Thread?, Edge finishing chrome-tanned leather and Gluing VegTan Leather to Polypropylene Plastic
-
Now this isn't pure chrome tanned (exterior: Vegetable tanned, interior combination tanned) but this is how I do my edges. And the second link a wallet that have been used for six years and edges still look nice.
-
I thought I share this. The only thing really expensive here is the electric creaser and Ksblade irons, but the same result is possible with cheaper alternatives as mentioned.
-
Gluing VegTan Leather to Polypropylene Plastic
Danne replied to PAMuzzle's topic in How Do I Do That?
Yes this is a better choice than Renia, I didn't think about the fact that it doesn't have to flex -
Gluing VegTan Leather to Polypropylene Plastic
Danne replied to PAMuzzle's topic in How Do I Do That?
Renia Ortec seems to work fine with polypropylene plastics. I can't try it right now since I'm not home. http://www.renia.com/englisch/material.html -
That sounds awesome, It would be amazing to visit a tannery. I guess I should visit Tärnsjö tannery in Sweden someday.
-
I try to share when I can. When it comes to some parts of leathercraft, fine leathergoods in particular, there is so much that are kept secret. I’m in no way an expert, but I have learned a lot of techniques over the years, and if I can help someone I will.
-
I don't think you will be disappointed, I have the V1 and they are awesome. The holes from Kevinlee premium is as good as Ksblade, but the advantage of Ksblade is their ergonomy, and also very easy to align against a scribed line, since the prongs are slightly rounded at the end. Edit: I saw you wrote diamond, I have the French irons, but from what I've seen on Instagram their diamond stitching irons are also awesome.
-
Sorry for late answer. Bees wax give a little bit more gloss to the edge compared to paraffin. Both work fine to seal the edge though.
-
I agree completely here. Ritza25 might be one of the most durable thread for a leathergood like a holster, but it doesn’t mean it’s the most suitable for a slim wallet or watch strap. It would be like saying ”A SDS rotary hammer drill is the best drill” Sure it can be true if you drill a lot in hard concrete, but it would certainly not be the best drill for someone who put up some shelves in their apartment with drywall.
-
And if I'm not completely wrong, the producer of Yue Fung's thread is Meisi. Meisi also have a nice sample pack so you can try their different threads. My favorite is Meisi Xiange twist, it looks very similar to linen thread, but it's a synthetic thread so durable over time when used for wallets and other things where friction cause the thread to tear when linen is used.