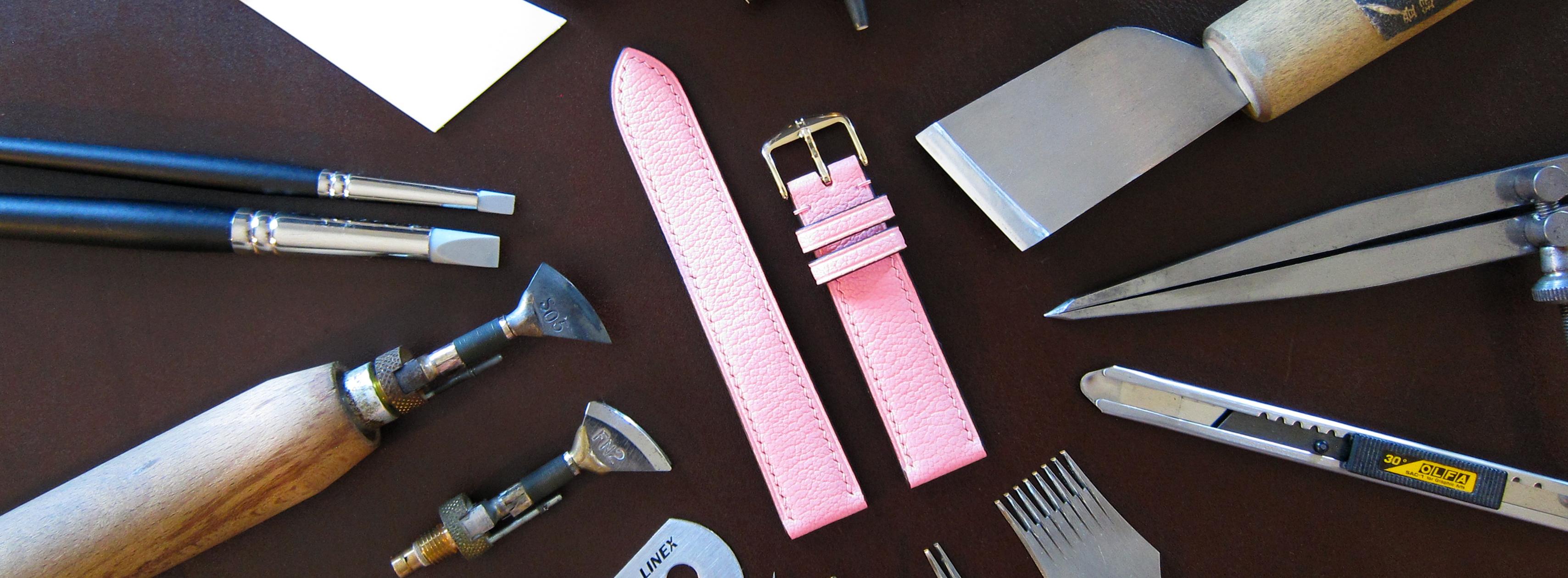
Danne
Members-
Posts
772 -
Joined
-
Last visited
Content Type
Profiles
Forums
Events
Blogs
Gallery
Everything posted by Danne
-
I add something here regarding the awls. I didn't like using awls before, because I could never get a good result. But at the same time I knew that for making wallets with skived edges and to get a good result I need to learn how to use an awl. Finally when I figured out how to reshape and sharpen my awls I was surprised how easy it was to get a good consistent result, and now I use it for all my wallets and card holders.
-
I'm curious what made you decide to go for Blanchard? Do you have Wuta European pricking irons now, do you think Blanchard will give you a better more consistent result? I only make wallets/card holder and watch straps. I have Ksblade 2,5,10 And the irons I have from Kevin Lee is 2 and 8. So I would say 2 + 8-10 works perfect for wallets, if I made bags (and only bags) it would be nice with more teeth.
-
I have Renia's thinner, bu still stringy. Don't get me wrong here Colle is a good glue, but in my opinion not the best choice for small leather goods, maybe more suited for a cobbler or something. I had Syntic Total in a "lid jar" with a diy gasket for months now, and use it rarely and in small amounts when water based glue isn't enough. And I think (don't quote me on this) that you can thin it down with acetone (If you are curious just check Renia's website, and the document for that glue)
-
I find Colle de Cologne super hard to work with because it's so stringy. (Even after it's thinned out) Renia Syntic Total and Renia Ortec are two alternatives I think you should try. My favorite is Syntic Total.
-
The few times I have burnished edges, I have used Fiebings oil dye (don't mix it up with Fiebings edge kote, which is in my opinion a edge paint that is not that durable) You might want to burnish the edge with water one time before you dye the edge. It depends on if you crease the edge or not, and what type of creaser you use. The creaser iron I used here round off and "seal" the edge transition which make it possible to dye the edge before burnish. But if your edge is just sanded your dye might seep up into the surface of the leather if you don't burnish the edge first. If you want to try painting edges I have a tutorial for this here. There are a couple of popular brands for edge paint, but I have only used Fenice and Uniters and I use the same technique with both of the brands.
-
This is how I do it, when I burnish edges. But I prefer to paint my edges with edge paint. 1. Make sure you don’t use too much glue, use water based or solvent based contact cement and a thin layer. If you need, you can prime with a thin layer, and add another. But NEVER a thick layer of glue. Press together really firm. 2. Let dry (time depends on glue) if you don’t let the glue cure, you will push in the glue when you burnish and get a very visible glue line. 3 Flush cut or sand edge flat. 4. Bevel edge. 5. Wet the edge with water (use a brush) to raise the fibres for later sanding, and let dry. 6. (Optional) Crease 7. (Optional) dye edge, I didn’t do this on the test piece here. 8. Wet edge with water and burnish with canvas or other heavier fabric. 9. Sand with 800 grit. 10. Put a burnishing agent on the edge, I prefer Tokonole. And burnish. 11. Burnish with canvas or other heavier fabric. 12. "Burnish" with 1200 grit sand paper (wet and dry) and keep burnish until your sand paper ”clogs up” don’t move it to fresh sand paper. When your sandpaper start to clog up you will burnish, you hear it on the sound from the friction. 13. Keep doing step 10-12 until all imperfections are gone. 14. Melt paraffin wax on the edge. 15. Burnish with a soft cloth (Like t-shirt) The edge is smooth as glass, unfortunately I can’t take any good photos that really show how smooth the edge is.
-
If you have decided that you want the European style irons, and want to spend a little bit more money on quality ones. I would recommend you to not choose pricking irons (Blanchard is an example of pricking irons, where the main purpose is to mark the hole and open it with an awl, because the prongs have a taper) But instead use "stitching irons" There are a couple of brands to choose from, I can only say my opinion about the irons I have. Ksblade and Kevinlee. Both of them give a very good result. Kevinlee is cheaper. Ksblade is ergonomically better (Kevinlee is a little top heavy) also Ksblade aligns easy to a scribed line. But i'm happy with both of the brands. In most cases I use them as somewhere between pricking and stitching irons when I make wallets, I pre-punch the exterior, and open up the holes with an awl after assembled. For watch straps I punch all the way through.
-
Mitsubishi question to the vendors of this forum
Danne replied to DrmCa's topic in Leather Sewing Machines
Maybe a really stupid question from someone who never owned a sewing machine. But how does that work, doesn't those "feed teeth" leave marks on leather? -
New 8 slot wallet
Danne replied to CastleLeatherWorks's topic in Purses, Wallets, Belts and Miscellaneous Pocket Items
Well done. Nice finish and I also like the combination of leather.- 11 replies
-
- linen thread
- buttero
-
(and 4 more)
Tagged with:
-
Renia Aquilim 315 and Ecostick 1816B are two popular water based contact adhesives. I use 315 and happy with that glue. (Haven't tried 1816B) A tip if you dilute 315 with water, use VERY LITTLE water. It requires very little water for thinning it out, and if you use too much you loose a lot of bonding strength. With just a small amount it's just as strong as new. (It get's a little thicker with time.)
-
I have tried a couple of different rotary punches and haven't been happy with them. A couple of years ago I found some old stock (New and not used) in a store here in Sweden from a company called Stahl in Germany. And have used this punch a lot and it's awesome. If you can find them online somewhere I would really recommend them.
-
I answered you in the other thread you made. You can make a nice edge with two coats of paint. I showed an example with Uniters EP-Full as a primer coat for the rounded shape, and one coat of Uniters EP-2000 A lot of manufacturers of edge paint sell those in different viscosity for different application methods.
-
Here is one coat of Uniters EP-Full, and one layer of Uniters EP2000. Started on a flat edge, and just dulled it a little bit with 800 grit. But the surface was the same. I have done some more tests with Uniters, and painting more layers with heat and sanding do give a better result (at least for me) but of course it's also more time consuming. EP-Filler (EP Full and EP-Filler = two different products) also seems like a good "primer" for the first layer, after I smooth it with heat it makes a very even edge to start with. But I let the photo talk for itself. An edge like this looks very good, especially considering how quick it is with only primer and one layer of paint. And of course it would be even quicker with a edge roller or edge painting machine (I used a round awl)
- 5 replies
-
- finishing edges
- finishing
-
(and 3 more)
Tagged with:
-
A lot of the big brands of edge paint have different viscosity to choose from. But keep one thing in mind when you see that thick one layer "rubbery edge coat" it's not that common it will peel off relatively easy. I have seen it especially on cheap handbags. I think Hèrmes use some version of Stahl (Have seen it in some of their clips) I now one really expensive high end brand use Fenice. (I don't think it's a secret but I won't mention the brand because someone who work their told me) If we take Uniters as an example. They have different viscosity of their edge paints. They also have a thickener you can add to your paint, and a filler. I have this filler in two version but haven't tried them yet, but I guess it's a product that can be used as the first layer and you only need one more layer for a rounded edge. I can update when I have tried these products. "EP FILLER is a water based polyurethane product with a high dry content designed to achieve a smooth rounded edge on bags, belts and shoulder straps in leather" Personally I would stay away from Fiebings edge kote. I have never seen a good result with that edge paint. Uniters, Fenice, Giardini, Stahl, Vernis600, Beraud CT are some of the more popular brands with good reputation.
- 5 replies
-
- finishing edges
- finishing
-
(and 3 more)
Tagged with:
-
New Wallet
Danne replied to CastleLeatherWorks's topic in Purses, Wallets, Belts and Miscellaneous Pocket Items
I took a cork sanding block and cut out a smaller piece and fold some sanding paper around that block. And sometimes I use sandpaper glued to a piece of stiff rubber mat. (You can see it in my edge painting tutorial here.) The only time I use a sand paper folded is the absolute last finish I often do with some 800 grit before melting paraffin and burnish. -
New Wallet
Danne replied to CastleLeatherWorks's topic in Purses, Wallets, Belts and Miscellaneous Pocket Items
Really clean. And your edges look good. If you want to improve them even more you don't need practice you just have to make sure your layers are completely flat before the next layer, and use a sanding block or something else so you avoid a "wavy" edge, because if the edge start to get a little "wavy" it's so hard to sand the next layer without sanding through. When I look at your wallet I see a really clean wallet with attention to details. And the contrast between EPI and chèvre looks awesome. Well done. -
1. Make sure to not use to much glue, if you use contact cement, use a thin layer of glue on both pieces, and make sure to press or punch the edge with a hammer. 2. Let it dry before sanding and burnishing, or you will push in the seam between leather layers. (Flush cut the edge is also a solution for a clean edge) 3. (I'm no expert on burnishing since I paint my edges) but I get good results when I 1. Sand or flush cut. 2. burnish with water. 3. Sand 4. burnish with Tokonole. And I keep doing this and use finer grits of sandpaper as the edge gets more uniform. And if I have painted that edge with oil dye, I almost can't see the glue line between layers. I can show you photos of some tests I did recently this this method?
-
I would recommend you to start with smaller items. Even if it's just test pieces. Because when you start to make bags, mistakes cost a decent amount of money because of the amount of leather. Someone asked me something along the line "How is it possible you have improved so much but not made a lot of things" (Keep in mind I do wallets and watch straps and small things) and I haven't done a lot of finished products, but I have done A LOT of small pieces. Like glue together two small scrap pieces, stitch it, crease it, bevel the edge and paint the edge. This way I now I feel confident in the techniques needed when I make that wallet or watch strap. Sure a watch strap is very little material cost, but it's not fun spending hours on a watch strap and making a mistake that ruin it because I lack experience of a certain technique. So in your case, I would use scrap leather and do test pieces of bag corners, maybe if you use zippers, just take two smaller pieces of scrap leather and stitch in a small zipper. Maybe the next step can be to make a dopp kit?
-
I think you made a good choice. I guess you bought a regular HDPE-board, not specifically made for dye cutting? And my guess is that those Hydroma boards I linked too cost a lot more, and for a company that use them like eight hours a day it can probably be worth spending the extra money, but for more "normal use" my guess is that your board will do the job for a long time (Amateur thoughts here, because I have no experience with dye cutting)
-
Check if they have a reseller where you live. https://www.roechling-industrial.com/products/thermoplastics-machined-components/soft-material-cutting-boards
-
I have glycerine based saddle soap, and also Sedgwick leathercare. Why would your products be more suitable in this case? Sully is a finished leather, and I was forced to use a strong cleaner to remove stains (Saphir Renomat in this case) I have very little experience regarding those products. But I know that Saphir Renomat is a stronger cleaner, I also know that my Sedgwick is not suitable for finished leather (at least not when I have tried on Sully)
-
It's 2.5 years old. It did dry and it feels like normal now. I don't have any beeswax in "liquid" but I have carnauba creme, I will do some tests on scrap pieces. Thank you.
-
It did dry and it's not sticky anymore, but it took a while. I will update here when it have been used for a while again.
-
Recommend a tool you like that is not mainly used for leathercraft
Danne replied to Danne's topic in Leatherwork Conversation
That seems like an awesome solution.