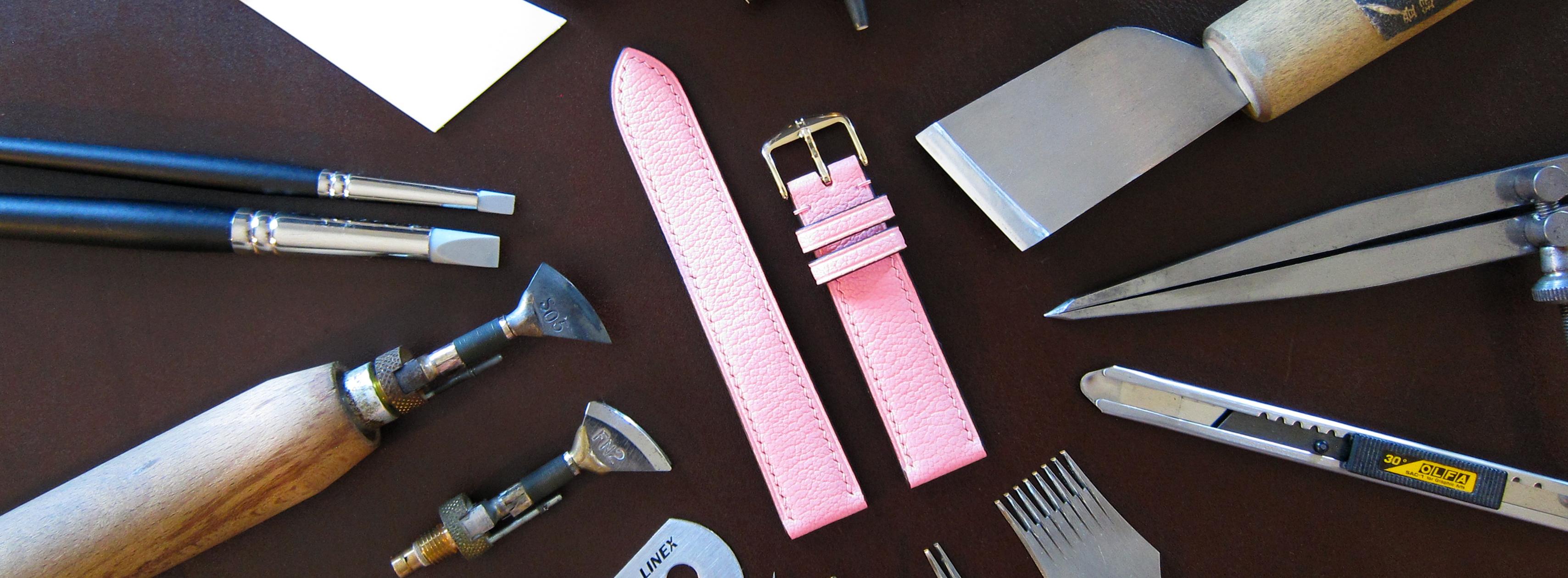
Danne
Members-
Posts
772 -
Joined
-
Last visited
Content Type
Profiles
Forums
Events
Blogs
Gallery
Everything posted by Danne
-
Watch bund strap
Danne replied to Danne's topic in Purses, Wallets, Belts and Miscellaneous Pocket Items
Thank you Spyros, Yes, there are a lot of tasks that is really hard on a strap like this. First cutting the relatively thin and not really firm leather close to exact dimensions. Second position the folds for the lugs in the correct position so the strap folds nice around your wrist and in combination with the part of reinforcement that have to be glued in a fold around the lugs. -
Watch bund strap
Danne replied to Danne's topic in Purses, Wallets, Belts and Miscellaneous Pocket Items
Thank you Design is inspired by eatsleeplay on Instagram -
Slightly padded and reinforced. Top layer: Alran chevrè sully goat marine Padding: Alran chevrè sully goat marine Lining: Haas Zermatt calf natural Stitching: Meisi linen MS014 (M30/0.35mm), 2.7mm/10spi Edge paint: Fenice custom color. (I know the second hand doesn't match the color of the thread, but the clockwork is going to be replaced, and I plan to paint the second hand to a matching color.)
-
Thank you,
-
According to a nice French guy I talked to it's Haas Derby (Epsom) If I understood him correct. Just so you don't mix up two different glues here. Ecostick = water based, no solvents, so not toxic, apart from probably a smaller amounts of fungicides to avoid mold. I have no experience with Evo-Stik, but just by doing a Google search I see them i metal jars, which almost always means solvent based. What glue did you find. Keep one thing in mind, it's very easy to think "Oh Hermès use it, it has to be the best glue for me" What do you need from a glue? adhesion to the different types of leather you use, easy to apply, no need to keep it in press (just assemble and use a roll or hammer), no strong solvents if not needed. This was examples of what could be your criteria when searching for a glue. For Hermès it's different. First there can't be any strong solvents (even though there probably are situation where they need to use solvent based glues) but it wouldn't be a good solution for most things, because people would have masks, they would have to install special ventilation where they glue. Other things, how do they apply glue? I doubt they use a brush for bags, I would guess they use a glue that is thin or possible to thin down so they can spray it on. Also the strongest glue isn't always the best. I have no experience repairing or making handbags, but I have seen repair photos and clips online, and you need to take apart the bag to repair some things. If it would be glued with a strong solvent based contact cement it wouldn't be possible without destroying the bag. Just some thoughts. And I will never use anything but water based glues for regular leather, because I don't see any need for it.
-
compagniedestanneurs also sell grained calf in smaller panels which is nice for a small crafter (i.e no need to buy full skins. They call it Epsom which is Hermès brand name for Haas Derby from tannery Haas. I can't really find any information if compagniedestanneurs is a tannery or a reseller, and if this leather is from Haas or if they just call it Epsom (because most people now that leather type as Epsom) I don't speak French, if this leather is something that is suitable for you, and maybe you check their site or get samples, I would be very thankful if you updated me, if it's not Haas Derby (Epsom) how is the leather, what temper, full grain? and such.
-
You said you planned to use Renia Colle (If you do, then use a respirator, because of the solvents.) But do you really need a solvent based glue? The only time I use solvent based glues are when I use synthethic reinforcement. Water based glues as really good, and very strong when used as contact cement. For example. Peter Nitz used Saregum 130 for both bags and wallets (He often used it for alligator/crocodile and chevre) for years with good result, he recently changed to Ecostick. But Saregum will work fine for regular leather (you might need a solvent based glue if you work with really oily/waxy leathers. Are you going to stitch your edges, if yes then you certainly don't have to worry. A couple of alternatives in France: Saregum 130: https://mando.fr/index.php?dispatch=products.view&product_id=2128 Aquagum 018: https://www.cuirtextilecrea.com/colle-contact-aqueuse-aquagum-018-500-ml-c2x26994292 Ecostick resellers in France: d.kermarec@compagniedestanneurs.com and contact@eprose.fr
-
French Edge Skiver - is this going to be a problem?
Danne replied to Alaisiagae's topic in Leather Tools
I think there is a big misconception that it's hard to skive with a regular skiving knife. Does it require some practice, sure like all things you do in this craft. But just like the awl I didn't like the skiving knife at first, because I never got good results. What was the reason? my tools wasn't sharp enough, and I also used the wrong technique. I tried to push the skiving knife through the edge, instead of using a sawing motion and doing the skiving in multiple skives. I have a tutorial here for skiving edge pockets, i'm no expert, but this works really good. Sharpening with wet and dry sandpaper of good quality on a flat surface (glass or granite) will work fine with the grits you use, I sharpen my skiving knives, french edgers and awls up to 2500 grit (Mirka sandpaper) and finish with green chromoxide on a strop (relatively stiff leather with the grain side up) and it cuts everything from soft 0.5mm leather up to thicker veg tan like butter. There are also sharpening guides you can use. Look on Etsy (If you don't find it, ask me here, and I find it for you) -
Is it possible to mould chrome-tanned leather?
Danne replied to ScottEnglish's topic in How Do I Do That?
Do you think that's the reason Hermès used what looks like veg tan in between the gator and Zermatt calf? to keep it's shape better when dried? Btw, your result was really nice, I might need a 3d printer now -
Is it possible to mould chrome-tanned leather?
Danne replied to ScottEnglish's topic in How Do I Do That?
This might interest you. At 1:49 they mold Alligator + veg tan? + Haas Zermatt calf. I have no experience with this, if the middle layer is veg tan, it might be to keep it's shape better? -
The strange part here is, I have no problem with this at all. A thin layer solvent based or water based contact cement and put together and hammer or press down the edges and let it dry before finishing edges. But I think the reason might be that all my leather is split down (In a band knife splitter) so the flesh side is very even. Also the thickest leather I use is 1mm. Like in my example it's two 1mm layers glued together and you have to look very close to see any line between layers (almost invisible)
-
For some reason I can't reach Giardini's webshop right now. But they have a product called Adhesion Aid.
-
Strange, I've had no problems like this. Not when used as contact cement or wetbond. Is it on oily/waxy leathers? I just looked through some old test pieces and found one glued together years ago and it's as strong as it was when I glued it.
-
I personally use water based contact cement for almost everything, the only time I use a solvent based glue is when I glue synthetic reinforcement. And if I would use oily/waxy leather I would probably use solvent based glue or Aquilim 315 mixed with hardener. I use Water based: Renia Aquilim 315 (Can be used as contact cement and wetbond, but is stronger as contact cement) it's a really strong glue. Solvent based: Renia Syntic Total. Why not pick up some Saregum from Mando? I know Peter Nitz used that glue for everything before (wallets and bags) Now I think he have switched to Ecostick. Here are a couple of examples of good water based glues. Renia Aquilim 315 https://www.ds-leder.de/index_renia-aquilim-315-200.html Renia Aquilim GL (Longer working time) https://www.ds-leder.de/index_renia-aquilim-GL-200.html Saregum 130 https://mando.fr/index.php?dispatch=products.view&product_id=2128 Intercom Ecostick 1816B https://www.eprose.fr/ (Contact them, they are reseller for Ecostick in France) Seiwa Bond Ace https://leathercrafttools.com/item/9944/ (I don't know any source in Europe for this glue)
-
Where to find Riri zippers and hardware in Europe
Danne replied to ThoughtFission's topic in Suppliers
Mando.fr -
Made a simple template for a card holder, and thought I share it here. I haven't tried making it. Recommended leather weight 1-1.2mm (2.5 - 3oz) Stitching 3mm/9spi If you have any questions regarding how to construct it, just ask here in the thread. Print 100% landscape (A4) 2card_template.pdf 2card.pdf
-
But wouldn't Tokonole or Tragacanth cause adhesion problems for the glue? My example photo is two layers of leather, how did I avoid the line between layers? very thin coats of glue (water based used as contact cement) Sometimes it can be a problem if a slower drying glue is used, it's important to let it dry completely before burnishing.
-
Aacrack have both split suede, reverse suede and Nubuck.
-
First I have to say i'm no expert, I am a self-taught hobbyist. Not that it matters in this tutorial, the purpose is to get a nice result, and this is a nice result. (In my opinion) There is of course more than one way to skin a cat (of course not literally in this context) but if we are talking literally there is more than one way to skive a cow (in my example I use a vegetable tanned cow skin. So this is how I do it and it works for me. What do you need, except your card pocket you plan to skive? 1. A sharp knife, it doesn't have to be something expensive, you can get a good result with a skiving knife for a couple of usd/euro. But if you can afford it, I would recommend a knife with decent steel. A really cheap knife will have a bad edge retention and you will have to sharpen it constantly. I use a Kyoshin Elle. https://www.goodsjapan.com/kyoshin-elle-japanese-leathercraft-utility-skiver-beveller-leather-knife-angled/a-20860 2. Should you skive with the bevel down or the flat side down? I'm right handed and use the knife I just linked. And I prefer to skive with the bevel down, then I get a "fulcrum point" to angle my knife on. 3. Push or saw? I prefer to saw through the edge in multiple passes. So let's start. 1. Scribe a line where you want to skive. (I filled my line with a pen so you can see better) 2. Make a first light skive (sawing motion) from right (the corner) to left. And keep doing a couple of skives until you skived the edge. Let's say your leather is 1mm thick and now it's around half of the thickness (0.5mm) and you want it thinner, you can wait with this until you skived the "pocket ear" (because it will be easier to see with a clean edge) 3. Do the same on the "pocket ear" to stop the leather from sliding away you can use your left hand to hold it down with a glue spreader at a low angle (I'm right handed so I skived with my right hand) 4. If you need to skive more to get your edge thinner, you can do it know. And the finished result.
-
Hi LionCrownLeather, one of the reasons I never use a slicker is that my edges are rarely thicker than 2mm. (In some cases 3mm on watch straps) For really thick edges I can see the benefit of a slicker, even though I would probably use a cloth. I don't even like canvas, I prefer something a little less rough. I'm certainly no expert on burnishing dyed edges. But here is how I have done it the few times i've tried it. (Include a photo of a dyed and burnished edge with this technique.) 1. Sand edges flat, the choice of grit depends a little bit on the type of leather, a stiffer leather and a rougher sandpaper like around 100-200 grit works good. For medium soft and softer leather I prefer 400 grit (wet and dry, I use Mirka) Don't put to much pressure on the edge when you sand, then you "mush" the edge, if you do, just lay it flat and burnish the edge transition from both sides (to push down the edge) Also try to sand "across the egde" and not along the edge. (Finer sanding I do along the edge, rougher sanding across the edge.) Sand until you have a relatively flat edge. (Flash cut your edge and you don't need to sand at all. 2. Burnish the edge with water. (I use a brush and just brush on a small amount of water. 3. slightly sand the edge with 400 grit. 4. Dye your edge (Why did I burnish with water before dying? to avoid dye seeping over the edge to much, especially if the leather is not lined) 4. Burnish with tokonole 5. Sand with 400 grit 6. Burnish with tokonole 7. Keep doing this until you have a relatively good edge. And keep doing the same but with a higher grit like 800-1200. (Optional) 8. Melt bees wax or paraffin on the edge and burnish. But there are a lot of ways to burnish edges, both techniques and agents like with Tokonole, Saddle soap, Arabic gum or Funori.
-
Welcome Lasse, i'm also from Sweden. You can probably see in my post what leather I prefer for my work. Which one do you prefer the one with greased feel or the dry feel? I really like the dry feel version, and the semi-aniline finish is just awesome.
-
Yes maybe one some thicker stiffer leather. And also it depends on what a decent-looking stitch is. All leather behave different, you have different thickness. One side might be softer and the other stiffer. My opinion is that saddle stitching is the hardest part of this craft.
-
160g (thickest paper for my printer, I think this was some laser photo paper, but it doesn't matter) When I make the first product I usually just cut out the template a little oversized and tape it to the leather and cut. When i'm certain i'm satisfied with a template I print it and glue it to some thicker "card board paper" (I use a regular glue stick) Something like this.
-